3/24/2025
Recapping Indoor Ag-Con
Jennifer Polanz
It was another eventful Indoor Ag-Con, this year moving to the Westgate in Las Vegas, with a diverse lineup of panels and educational sessions, as well as the first Cultivating Excellence Awards (click the link to read the winners), a trade show floor of more than 300 booths and multiple co-located events. Attendance this year topped more than 1,600 people, which highlights continued steady growth. In fact, the show was just named one of the Fastest 50 from Trade Show Executive magazine. This is just a sample of what we heard, saw and learned at the show.
Keynote Panels
The two keynotes hit on where the industry is currently, as well as potential headwinds from threatened trade wars and tariffs. First the industry status. There is a concept that is often highlighted in the CEA industry called the Gartner Hype Cycle, which focuses on the five stages of the lifecycle of technology. Keynote moderator Tom Stenzel (executive director of the CEA Alliance, noted the industry is moving toward the Slope of Enlightenment, the fourth phase after the Trough of Disillusionment. Essentially, he said, as operations begin to replicate consistency, they can bring down costs, meet retailers’ needs and achieve unit economics, sending them to profitability.
Panelist Tisha Livingston of Infinite Acres and 80 Acres Farms noted the progress was slower than they thought on the vertical farm side because the technology still wasn’t quite there in the beginning, but they are now working to scale up profitably. “We knew it was going to be a bumpy ride,” she added.
80 Acres recently announced they bought three Kalera facilities, pushing them west of the Mississippi (they are based in the Cincinnati, Ohio area) into Colorado and Texas, as well as south to Georgia. The grower also purchased a biotechnology company called Plantae, which in part has breeding capabilities.
That was another message that was clear during the keynote and throughout the show: breeding and genetics are key factors in the success of indoor production, but the larger breeding companies haven’t dedicated efforts to indoor, instead continuing to focus on field production.
The second keynote panel focused partly on potential tariffs between the U.S., Canada and Mexico and the impacts of those on Canadian growers. Panelists obviously talked about headwinds, but there were also opportunities for those Canadian growers to fill shelf space that may be left empty from retailers not stocking imported produce.
The challenge is Canada imports the majority of its vegetables, with much of that coming from the U.S., and panelist Valerie Terrault of Gen V noted that biodiversity of crops will be key in the future. “If we’re all doing the same thing it’s not going to be good for our business,” she said.
Canada exports heavily to the U.S., too, and the panelists highlighted the need for increased efficiencies through automation, AI learning and improved genetics to make that more cost effective. Panelist Bahram Rashti from Up Vertical Farms also called for additional collaboration with government and universities on food security and to build local supply at home.
A final common thread was for the CEA industry in all areas to get more involved with their governments to show the benefits of indoor production and ensure the industry has a seat at the table when ag topics are being discussed. One way to do that in the U.S. is by joining the CEA Alliance, an organization that advocates for the industry, and another is to call and meet with your Senators and Representatives directly to advocate for indoor production. Inviting them on a tour of your facility is a great way for them to learn more about what you need to thrive.
New Tech
Walking the trade show floor we found a couple of interesting products and systems to highlight:
Purifico Ozone Products highlighted its ozone disinfection system as a way for growers of all sizes to treat water chemical-free to eliminate pathogens and organic matter. The system is essentially about the size of a refrigerator (more narrow, in fact) and is plug and play, producing ozone from oxygen using electricity and ambient air. The ozone dissolves into the water, and eventually converts back into oxygen. Ozone can improve plant health and lower disease pressure from waterborne pathogens. These are manufactured in Edmonton, Alberta, Canada, and some growers there are already using the system. The company has been mainly in the dairy industry until now, and they are looking for more distribution.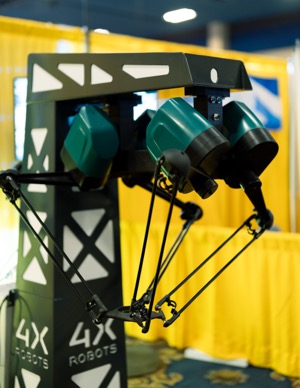
4XROBOTS caught our eye walking by as the robot arms methodically moved back and forth. What’s unique here is the robots are designed to be collaborative—to work alongside a human to make their job more efficient. It’s small, nimble, cost-effective and the center portion can be changed out depending on the application, making them accessible for a wide variety of tasks. It can be set up by two people and doesn’t have to be fenced off for safety, like some automation. The robots are built in and shipped fr
om Denmark.
While we were chatting in the J.R. Peters booth, they told us about a Strawberry Part A nutrient formulation in the Jack’s Nutrients line that had been developed by Dr. Chieri Kubota at The Ohio State University a couple of years ago that we haven’t yet reported on. The 8-10-26 formulation is attuned to indoor production of Albion and combines certain macro, secondary and micro nutrients for a low feed rate that complements the Jack’s Part B for calcium.
UK-based Zayndu is a company that makes a cold plasma seed treatment machine that they say increases crop yield by 15%. The machine creates a special environment by activating the air around the seeds, enriching them with oxygen and nitrogen. It doesn’t take up a lot of room and would be on site at the growing facility in a temperature-controlled location. Currently the machine can process 2.5 lb. of seed at a time, with four-hour cycle times allowing for about three cycles a day. A new machine, though, will be able to process 7.5 lb. per cycle in three-hour cycles, allowing for close to 25 lb. of seed to be treated per day. The machines are part of a subscription contract that would be either on a 12-, 24- or 36-month basis.
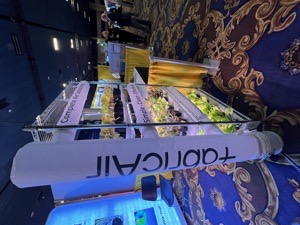
Fabric Air is a unique, lightweight circular polyester blend system that ensures uniform airflow over plants, removing microclimates. The company started in 1973 making these for indoor pools. They can be customized in size, colors to fit the growing space, and they can be used in multi-level growing facilities. They come with a 10-year warranty.
Not every growing operation has a wifi mesh system, or even if they do, it isn’t guaranteed to reach all corners of the greenhouse or farm. With that in mind, Growbud was showing an environmental sensor to precisely measure multiple growing factors and report back to a Lorawan Gateway, which is an ultra-long-range connection that spans up to two miles. The DRO Sensor measures volumetric water content (VWC), EC, air pressure, humidity and vapor pressure deficit (VPD).