2/1/2023
Making Sense of Sensors
David Kuack
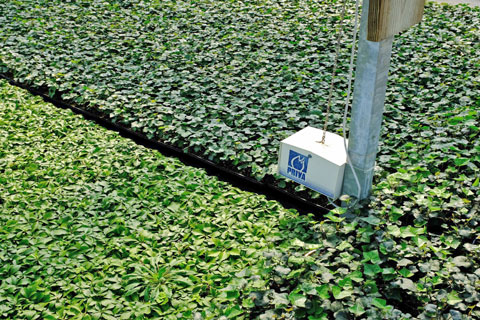
How are you using the data collected by the sensors that measure the environmental parameters in your controlled environment operation?
“Growers typically underestimate the value of data collected by environmental control sensors,” says A.J. Both, a greenhouse engineering professor at Rutgers University. “If growers collect the data, store them and use them, they can be a very valuable resource to assess how their environmental control systems are performing. This data can also be used to assess what growers might do differently in order to increase energy efficiency and/or increase the yields and quality of their crops.”
Pictured: Temperature and humidity sensors are often placed in an aspirated box, which shields the sensors from solar radiation and inadvertent water splashing.
One of the benefits of collecting this data is growers also have a record of when things go wrong with their control systems. A.J. says when something fails to operate properly, growers can quickly see in the sensor log if there was an issue with the temperature increasing or decreasing depending on what’s happening with the crop.
“Having a log with the time stamp can be very valuable when determining if something went wrong and that may help growers troubleshoot what they need to do to fix a problem,” he adds.
Choosing the “right” sensors
A.J. says the environmental control system used by a grower usually depends on the level of sophistication of the growing operation and the value of the crop being produced.
“If the plants are hardy and don’t require a lot of precise environmental control and the value of the crop is not particularly high, then a grower can probably use a minimal number of sensors to operate the control system,” he says. “If growers are investing a lot of time, effort and energy to maintain a particular environment for a crop that has a relatively high value, then growers may want to increase the sophistication of their sensor systems.”
The basic environmental parameters that are measured by controlled environment growers include temperature, relative humidity, light (photosynthetically active radiation), carbon dioxide concentration and substrate moisture content.
“The difference in the available sensors can be evaluated in terms of the quality of the data they generate,” A.J. says. “An inexpensive sensor may not hold its calibration very well or may not be calibrated at all. For the parameter being measured, the data may be sketchy or may change over time even though it is exposed to the same conditions when the sensor is drifting from its calibration. More sophisticated sensors typically cost more, but are made with higher quality components. Typically, that means the sensors are more stable and more accurate in representing the real circumstances that growers are trying to assess.”
A.J. compares choosing an environmental control system to purchasing a car, with a wide range of choices available.
“Growers looking for a basic control system may choose sensors for only temperature and relative humidity. From there, a grower can install more sensors and more parameters to control and measure,” he said. “This means investing more money in both the control system as well as in the individual sensors.
“Depending on what growers are looking for in regard to environmental control accuracy, and whether they are using carbon dioxide enrichment, will depend on whether they want that particular control feature as a component of their control system,” A.J. continued, adding that growers who are more concerned about the moisture content of the substrate will also want to know more about that parameter.
Bruce Bugbee, professor of crop physiology at Utah State University and president of Apogee Instruments, said light is the single biggest environmental parameter that growers aren’t measuring.
“Some growers are producing their crops without knowing whether their crops are receiving high light or low light levels,” Bruce says. “As more growers are installing LED fixtures, they are beginning to understand the value of light.”
He adds that one of the last sensors growers usually buy is one to measure light intensity, which is a problem because that’s the first sensor they should buy.
“They can get away with a growing media pH of 4 to 7. If they fertilize properly, they don’t necessarily need to measure electrical conductivity. They need to measure light, but don’t necessarily understand the need to measure light because they can’t see it,” he adds.
Sensor numbers and placement
The number of sensors installed should be based on the amount of variability in a particular growing area.
“If a fairly stable environment can be maintained, then having multiple sensors is probably not going to provide a lot of new information because the conditions are relatively constant throughout,” A.J. says. “If for whatever reason, there are production areas where it is much warmer or much cooler, then having sensor input from those locations in addition to general locations is a good idea. The information from these outlying areas can be used to decide how to handle these different conditions, especially when growing the same crop and all the plants need to finish at the same time.”
Pictured: Although the top of the plant canopy is used as a reference point, as plants become denser, the humidity could be higher inside the canopy, possibly leading to diseases such as Botrytis.
In order to properly measure the substrate temperature, a sensor is usually placed in the center of the growing medium where it can provide a good average temperature. A.J. warns that growers should be aware that when black plastic or dark-colored plastic pots are placed in a bright, sunlit greenhouse, there can be a significant heating of the growing medium near the sides of the pots.
“There can be a significant temperature range across the growing medium inside the pots if measurements are taken in multiple locations within the pots,” he says. “Therefore, it is important to put the sensor in a location that best represents the average conditions across all pots.
“This is similar to the decision where to place moisture sensors because the moisture level likely won’t be consistent throughout a substrate. In addition, water is a very good medium to contain heat energy. The lower the water content in a substrate, the less the substrate will be able to hold heat.”
Bruce said it’s rare that a grower would use too many sensors to measure a particular parameter.
“The first place to measure is at the top of the plant canopy,” Bruce says. “But that location changes with the maturity of the plant and change in height. Sensors will have to be moved as plants grow. Typically, the top of the plant canopy is used as the reference point.
“It is also helpful to measure inside the canopy because there is less air movement. The humidity at the top of the plant could be 60% and a grower might assume the plants are just fine. But when the plants become denser and there is inadequate air movement, the humidity could be 80% inside the canopy, possibly leading to diseases such as Botrytis.”
Sensor calibration and replacement
A.J. says just like other equipment, it’s a good idea to have a replacement schedule for sensors, noting it’s hard to predict their life expectancy. The greenhouse environment can be tough on equipment because of the relatively high humidity levels, he says, adding there’s also water splashed from irrigation, as well as chemicals applied to the plants that can also affect sensor performance and longevity.
Sensors typically need to be replaced when it’s difficult to recalibrate them in-house or when they need to be sent to the manufacturer more frequently for calibration.
“Previously sensors had to be recalibrated much more frequently,” Bruce says. “As sensor accuracy has improved, they have also become more rugged and more stable. Sensors that had to be checked for accuracy every year can now go every five years, and some even longer, and still be reliable and stable. This varies with the type of sensor.
“Sometimes growers use redundant sensors to make sure they are measuring a parameter properly. This can be a good approach. If growers only have one sensor, they want to make sure the parameter is measured correctly. Sending a sensor back to the manufacturer for recalibration or testing is always best, but that is also the most time consuming and the most expensive way.”
Using sensor data
It’s common for growers to look at their control computer first thing in the morning to see if there were any anomalies in the data that was recorded overnight.
“Especially during colder nights, growers want to make sure temperatures don’t get out of range,” A.J. says. “If there was a deviation from the set temperature range, growers need to know by how much, so adjustments can be made in order to correct any negative consequences for the plants. This is an example of the immediate use of recorded data.”
Because the data can be stored, such a record can be a valuable tool later when growers want to assess what happened during the entire growing season.
“Another good comparison is when growers want to compare the current crop that is being grown with a similar crop that was grown last season,” A.J. says. “This enables growers to look at the differences in environmental conditions and whether those conditions explain why there may be differences in growth between last year’s and this year’s crops.”
David Kuack is a freelance technical writer in Fort Worth, Texas. He can be reached at dkuack@gmail.com.
More Sensor Details
A.J. Both presented a webinar on “Environmental Sensors 101” on November 15, 2022, during the 46th Indoor Ag Science Café organized by the OptimIA project team, which is funded by a USDA Specialty Crop Research Initiative grant.
https://www.scri-optimia.org/showcafe.php?ID=111164